Renault fait entrer ses usines dans l'ère du tout numérique
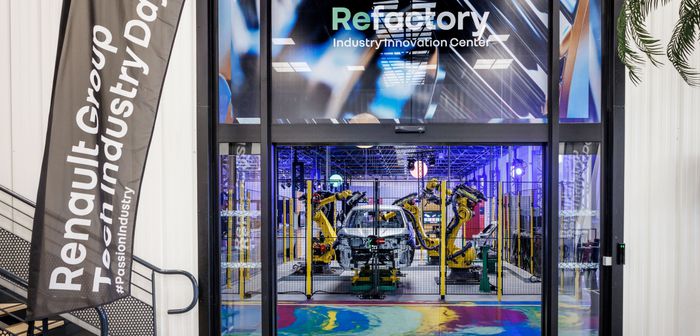
Mardi 24 octobre, sur le site de Flins en région parisienne, Renault nous avait invité à découvrir sa transformation numérique. Au premier abord, le constructeur a choisi d’en mettre plein la vue, du bon marketing à base de "métavers", d’avatar numérique, de twins, de la sacro-sainte IA vendue un peu partout, d’assets, etc. Pour entrer dans le monde 4.0, il faut savoir parler anglais sans quoi, l’aspirine peut devenir son meilleur ami.
Le métavers, est devenu à la mode depuis que Facebook a décidé de renommer sa plate-forme. Et si Renault communique ainsi, c’est bien pour montrer qu’il entre dans une nouvelle ère, et prouve sa transformation à travers la numérisation de ses usines. Est-ce la Renaulution annoncée par Luca de Meo l’année dernière ? Oui et non.
Ce projet a en réalité débuté il y a 5 ans, sous l’ère Carlos Ghosn, avec un investissement annoncé de 30 millions d’euros par an. L’objectif de Renault: numériser totalement toutes ses usines pour gagner en efficacité et bien sûr réduire les coûts. Au passage, la notion écologique devenue très importante de nos jours est également au menu. Cela tombe bien. Ce projet est devenu réalité il y presque 3 ans, en 2019, et depuis, les différents sites de Renault dans le monde migrent dans l’ère du tout numérique.
Collecter un maximum de données issues des machines outils
Là où le terme de metavers prend tout son sens, c’est bien dans la collecte de données. Contrairement au réseau social américain qui a lancé la mode de ce terme, ces données ne sont pas personnelles, mais bien industrielles. Pour faire simple, Renault a fait en sorte que les innombrables machines parlent le même langage ou plutôt, que leur langage soit traduit dans un langage commun, pour ensuite pouvoir les traiter, les analyser et prendre les mesures qui s’imposent.
Pour cela, Renault a développé en interne une plate-forme appelée IDM4.0 (Industrial Data Management Platform 4.0). Le stockage des données est réalisé dans le Cloud de Google, un choix qui peut tout de même poser question à l’ère de l’espionnage industriel.
Ainsi, ce sont désormais 8 500 équipements qui sont connectés dans le monde, et plus de 60 procédés de production modélisés en numérique (soudage, vissage,...) qui remontent chaque jours, plus d’1 milliards de données.
Pour faire simple, les machines font parvenir en temps réel les données de leurs différents capteurs à une interface qui stocke de façon ordonnée ces datas dans une base de données. Étant donné la multitude de machines qui disposent toutes de leur propre langage selon les générations, les marques, les modèles, et leurs spécificités, Renault a dû développer pour chacune d’elles des solutions spécifiques représentant des milliers de lignes de code informatique.
Ces solutions stockent ensuite les données récoltées de façon unifiée, de sorte qu’une interface puisse ensuite interpréter ces données et les mettre à disposition des équipes.
Cette collecte de données, permet ainsi de pouvoir comparer les machines des différentes usines dans le monde et ainsi de corriger celles qui semblent dévier. Cela permet d’améliorer la production, d’anticiper et réduire la maintenance et d’optimiser leur fonctionnement. Et donc au final, de réduire les coûts.
Depuis 2019, selon Renault, 300 alertes ont déjà été détectées, permettant d’éviter ou de réduire des arrêts de production.
Réduction de la consommation énergétique
Même chose sur le plan de la consommation énergétique: en disposant de toutes ces données, le constructeur peut identifier les pertes énergétiques. Un exemple concret, quand une chaîne est à l'arrêt, le système permet de détecter une consommation résiduelle anormale et de lancer l’alerte. Autre exemple, un système mal réglé ou déréglé va forcer davantage. Outre le fait que l’usure sera supérieure, entraînant un arrêt pour maintenance plus tôt que prévu, la machine va également surconsommer. Ce système permet de détecter toute anomalie en ce sens.
Renault s’associe à Atos pour commercialiser son produit
Fier de son outil, Renault s’est allié à Atos pour commercialiser sa solution pour d’autres industriels, pas forcément dans le monde de l’automobile d’ailleurs. Car sa solution peut être déployée chez tout industriel qui souhaite mieux superviser ses usines. ID@Scale, c’est son nom, devrait d’ailleurs être prochainement déployé chez un premier client européen. Renault déploie là sa nouvelle stratégie commerciale en n’étant plus “seulement” un constructeur automobile, mais également un concepteur de solutions à destination de l’industrie. Un vrai changement de paradigme.
Une chaîne de fabrication connectée et mieux contrôlée
Sur les chaînes de production, le papier a totalement été remplacé par le numérique. Il était temps pourrait donc dire à l’ère du 100% numérique. L’ouvrier sur la chaîne est ainsi équipé d’une tablette qui lui permet d’être en relation continue avec son chef d’équipe, et qui lui indique également toutes les informations à connaître, point d’attention, ou problème.
Pour aider les opérateurs et détecter les erreurs potentielles en amont, différentes caméras analysent et détectent de potentiels problèmes, notamment dans la logistique. Pour illustrer son propos, Renault a notamment présenté la solution Pokaiok Wheel Concept qui vise à s’assurer que les deux pneus sur le train avant et train arrière sont identiques. Pour ce faire, une caméra va lire la référence des pneumatiques et lancer une alerte en cas d’erreur détectée. Si Renault a parlé d’IA pour vanter les mérites de son produit, il ne faut pas s’y tromper. L’intelligence artificielle n’est qu’un terme marketing pour parler d’un logiciel, qui agit selon un des règles informatiques codées par son développeur, que l’on appelle un algorithme. La véritable IA n'existe d’ailleurs pas. Bref…
Si on met de côté l’IA, cela peut paraître simpliste, mais de nouvelles normes imposent de pouvoir prouver que les pneus sont bien identiques. Avec ce dispositif, le contrôle est facilité tout comme la traçabilité qui est désormais réglementairement exigée.
Une formation numérique
La formation des équipes est également un point important de la numérisation. Ainsi grâce à la réalité virtuelle, les équipes peuvent se former sur site et dans des conditions similaires à la réalité. L’exemple donné était un atelier de peinture.
Le système reproduit l'environnement de l’atelier de peinture dans lequel va officier l’opérateur. Muni d’un gilet spécial et d’un casque de réalité virtuel, le système est capable de modifier la lumière, de détecter les erreurs de manipulation, les zones où la peinture est manquante ou trop importante afin que l’opérateur puisse travailler ses gestes. Une solution qui serait bon de proposer aux particuliers qui veulent repeindre leur voiture tant le "coup de main" n'est pas évident.
Selon l’équipe présente, un opérateur peut effectuer toute sa formation avec ce dispositif et aller ensuite directement sur la chaîne de production.
Une logistique renforcée et mieux contrôlée
Sur la chaîne de la logistique, la fameuse “Supply Chain” qui claque si bien à l’oreille, toutes les voitures sont désormais tracées en temps réel, permettant de mieux estimer les délais de livraisons et d'assurer un meilleur suivi.
La gestion des pièces détachées est également améliorée, permettant un meilleur suivi du stock, de réduire ce dernier, et d’assurer de meilleurs délais de livraison.
Avec cette numérisation massive, Renault espère économiser chaque année 320 millions d’euros en production, et 260 millions sur la Supply Chain, pour un investissement de 30 millions d’euros par an depuis 5 ans. De quoi améliorer sensiblement ses marges et son chiffre d'affaire.
Renault a également profité de cet évènement pour nous présenter de nombreuses évolutions ou innovations à venir, comme les opportunités offertes par les différentes techniques d’impression 3D, son futur moteur EESM, les évolutions sur les disques de freins pour réduire les particules de freinage, les nouvelles techniques pour les structures en aluminium, le futur des batteries, etc. Nous vous ferons découvrir cela dans un futur article.